The topic of this article is the painting of metal products in a production environment. The material brought to the attention of the reader, of course, does not pretend to fully encompass all possible solutions: within its framework, we will only get to know a couple of technologies that are widely used in modern industry. We will study the powder coating of metal products and hot dip galvanizing.
My knowledge is based solely on my real life experience with the products and situations discussed above, and not on any formal training. Please use this information as a starting point for your project, but discuss with your local paint representative before proceeding. The picture of hot dip galvanized steel is an orthodox and well-established practice in the external environment, both in Australia and internationally. However, there are examples of early failure of galvanized paints due to improper performance and poor practice.
Requirements
Industrial coatings combine two functions: decorative and protective.
What paint can protect metal products from?
- First of all, from corrosion, transformation into unstable oxides upon contact with water and atmospheric oxygen.
Useful: not only black steel is subject to corrosion. Electrochemical corrosion of aluminum, for example, comes down to the migration of charged particles from its surface. For the process to occur, it is enough to place any copper product together with aluminum in an electrolyte (say, water rich in mineral salts).
The cost of powder coating MDF boards
This manual is aimed at preventing such failures by sending specifiers and applicators to paint systems, surface preparation and application practices that will ensure the durability of the paintwork in a wide range of operating conditions.
Despite the fact that good coloring methods and general products have been assigned for different exposure conditions, this does not exclude the possibility of satisfactory performance of other paints and techniques. However, when choosing alternative products, specifiers are strongly advised to select products only from those with proven records of satisfactory long-term performance under equivalent or more severe service conditions.
- In addition, paint and varnish coatings protect the metal from contact with aggressive media present in many industries.
- Finally, they provide basic protection against mechanical damage. This property is especially true for soft metals (the same aluminum).
Technologies
Let's move from studying theory to getting to know practice.
Hanging metal products into the transport system
This document is only general guidance and requires strict adherence to separate paint manufacturing instructions for each patented product. The reasons for the painting of galvanized steel are mainly. Decorative - to create an aesthetic color and shine or to provide an identification color. Higher chemical resistance - in a situation where only galvanization can be vulnerable, for example, outside the pH range from 6 to. Increased durability - longer life. . In outdoor services that are remote from the coastline and isolated from areas of serious industrial pollution, hot dip galvanizing is durable in nature.
Powder coating
Benefits
What makes powder coating of metal products so popular?
The list of advantages is quite large.
- Powder coatings are extremely economical. Unlike traditional painting with a hand tool and especially pneumatic spraying, the loss of coloring material is reduced to almost zero. Most of the powder is deposited on the surface of the painted product; that part of the dye that wakes up during application can be reused.
- Powder coating of metal products does not require the use of solvents, which are used only as a carrier for pigments. Moreover: atmospheric pollution by their toxic fumes is excluded, which positively affects the environment and eliminates harm to the health of workers.
This contrasts with paints and other organic materials that are degraded by solar radiation. In benign internal situations, and especially in conditions of extreme exposure or wear, unless a change in color or gloss is considered necessary, galvanization is usually best left unpainted.
A large amount of galvanizing is painted at random, with regular latex or a suitable solvent-based alkyd primer 3. Choosing this primer is crucial and requires a clear recommendation from the paint manufacturer. In particular, the use of an alkyd primer in direct contact with galvanization can lead to stratification of the paint due to its saponification.
The dye consists of one component - a pigmented polymer powder.
- before receiving the finished product - takes a minimum of time. The coating is applied in one coat.
- The dye does not require preliminary preparation and dilution, does not thicken over time and has an unlimited shelf life.
- The process can be fully automated, which implies a stable quality of coverage, regardless of the professionalism of employees.
- The protective layer is practically devoid of pores. The reason has already been mentioned - the absence of solvents that evaporate during the drying process.
- Finally, sagging and uneven coloring are not possible due to the technology used.
The price of painting a running meter of a profile with a cross section up to 30 mm is about 20-27 rubles, a cross section of 60-250 mm - 50-55 rubles.
Equipment for powder coating of metal products
It is important to note that since these coloring systems are quite thin, usually from 70 to 120 microns for a three-layer system, the zinc profile and localized areas with increased zinc thickness, for example, at the edges, can be seen on the surface, just as the grain is visible in painted wood. Although this has rarely been a problem, higher inks can be used as part of the paint specification.
Painting for increased durability
Recognizing lower user requirements for conventional decorative paints, strict adherence to proper surface preparation and the specification of the base coat is the key to reliability in all galvanizing situations. Hot dip galvanizing is inherently very durable, so it is rarely required to paint it to achieve its intended life. Indeed, in areas with higher corrosive activity, the painting of galvanized steel can actually accelerate the corrosion of the zinc substrate and reduce the overall service life of the product from the expected service life only in the galvanized state, unless a reasonably selected, uniformly applied system with high assembly and integrity from this The paint system is maintained through its service life.
Technology
What does the powder coating process look like?
The most laborious part of the job is surface preparation. It consists in the complete cleaning of dirt, rust and old coatings. In industrial conditions, sandblasting machines are usually used for this, using airborne silica sand as an abrasive.
However, in conditions where the galvanized coating is slowly exposed to an aggressive environment, the use of a suitable coating that isolates zinc from this environment can extend the life of the galvanized coating. Therefore, under severe operating conditions in coastal and industrial conditions, the galvanization pattern can significantly extend the service life. Even in fairly mild outdoor conditions, where galvanization can continue for decades, it may be wise to paint areas that are protected from the cleaning effect of rain in order to extend the life of the structure even further.
Curious: in the case of preparing complex surfaces, a significant part of the work is done by hand, using a hand-held power tool.
Before painting, the surface is degreased with a solvent. And this work is often done manually - with the usual rags.
The paint systems described in the “Service Requirements 3 to 5” section are essentially paint systems designed to provide enhanced durability, wear and tear resistance, and more aggressive atmospheric conditions. Paints range from two-component epoxides and polyurethanes to powder coatings. Most paints have certain restrictions on how to apply and cure them, and these restrictions must be strictly observed. Powder coatings because they harden once they are clogged can offer material benefits.
An alternative method of surface preparation, involving a large degree of automation, is etching with solutions of acids or caustic soda. However, after their use, a thorough washing of the metal is required.
The painting process itself consists of two technological operations.
- Electrostatically charged powder is sprayed in a chamber equipped with filters for trapping it using manual or automatic spray guns. Thanks to static, it evenly settles on the surface of a grounded part.
The cost of powder coating corrugated products
In addition, since they can be applied electrostatically, a more uniform coating can be achieved with complex shapes than is possible with conventional paints. However, a reasonable choice of pre-treatment and application by competent operators is critical to productivity. For effective galvanization protective coatings, the thickness of the paint system should be increased as the environment becomes more corrosive. For painting under conditions of high corrosivity, where it is difficult to guarantee the thickness and integrity of the coating, it may be necessary to avoid galvanization and look for an alternative corrosion protection system.
- Then the painted product is transferred to the furnace, where at a temperature of 150-200 degrees the coloring powder is melted, forming a monolithic coating, and polymerizes. After cooling in air, the product is ready for shipment to the customer.
Hot dip galvanizing
This type of coating is usually applied solely for protective purposes: the decorative properties of galvanizing, frankly, leave much to be desired. However, galvanizing provides exceptional strength and durability of protection: from 65 years in an industrial environment to 120 when used in domestic conditions.
Another prerequisite is the selection of a suitable corrosion inhibitor. Indeed, many failures of paint systems compared to galvanization can be traced either to an inappropriate primer or to an inadequate overall paint thickness 6.
Examples of metal painting work
The paint systems described in detail in the “Service Requirements 3 to 5” section also provide options for situations where aesthetics are required. In those cases where the surface is protected from the cleaning effect of rainwater, which would otherwise wash away contaminants from the surface, uncoated steel and galvanization are more susceptible to corrosion than other corrosive metals. Corrosion in these sheltered places, for example, under verandas and open covered areas, can usually be 3-5 times greater than for surfaces exposed to rain.
On a photo - risers of water supply from a galvanized pipe after half a century of operation.
Benefits
- Corrosion resistance of metal during hot galvanizing approaches the resistance of stainless steel and far exceeds all paint coatings.
Curious: with minor damage to the protective or protect in other ways. The instruction is related to the ductility of zinc and its tendency due to electrochemical processes to be independently distributed on the surface of steel at a speed of about 2 millimeters per year.
In such cases, the appropriate paint systems described in the “Service Requirements 3 to 5” section should be taken into account, and the paint system should extend beyond the microclimate by at least 150 mm. This added coating isolates galvanization from accumulated contaminants. Since this layer is not directly exposed to sunlight, a two-component epoxy primer will be quite durable.
In a similar vein, while a galvanized structure can be substantially exposed to the atmosphere, in some places it can come in contact with the ground, burrow into the soil or undergo periodic or continuous separation of rainwater. In such situations, localized painting or the use of protective tape or wraps may be required to avoid premature corrosion in these areas. Again, the protective coating should go far beyond the microclimate.
- Zinc film is much more stable than any paintwork materials in relation to impact effects.
Technology
- Preparation of the product for galvanizing is reduced to its etching with an acid solution and washing with plenty of water.
- Then it is loaded into a cylindrical drum and immersed in a bath with molten zinc. The rotation of the drum creates a melt flow, uniformly filling all the irregularities and pores of the metal.
- The drum is removed from the tub and spun to remove excess zinc due to centrifugal forces.
Painting for enhanced chemical resistance
This includes exposure to strong acids and alkalis, as well as salts of strong acids and weak bases, and vice versa. Galvanization can also catalyze the degradation of certain organic chemicals that are exposed. This phenomenon is rare and does not prejudice galvanization. Just as coatings provide enhanced protection in aggressive atmospheric environments, smart paint systems can also protect galvanization from aggressive chemicals. Such approaches are usually taken only where the chemical effect is low or moderate.
Conclusion
As already mentioned, we have described only two technologies among countless industrial painting methods ().
In the video in this article, the reader can find additional useful information. Good luck!
Powder coating is an effective method of protecting metal and products from corrosion and environmental influences. Painting is economically advantageous. The technologies are practically non-waste; modern European equipment is used at work. All this provides affordable prices.
Otherwise, the safe principle of adoption in conditions of extreme exposure is the use of a substrate material, which is inert in essence. In such situations, stainless steel and plastic composites often find an advantage.
For specific chemical exposures, you should always seek expert advice or an established successful medical history 7. We provide high-quality blast cleaning. It can be designed and adapted to a range of shot blasting applications, whether industrial or commercial. It does not matter if your project is a small metal facility or a large industrial building complex, we have the right people and the right equipment to provide you with the highest possible shot blasting service.
LLC PP MetStroy provides powder coating services for any metal products up to 12.5 m
We offer a large selection of additional services. At the request of the client, we can pack the goods. We select colors and materials. In the work we use only imported paint, as a result, we obtain the ideal quality of painting flat products. The company has its own engineer, who understands all the intricacies and nuances of work. We use only high-quality products, this allows us to give a guarantee on all work performed.
Steel shot blasting is a high-quality abrasive for a number of different things, it is a sustainable method, which means that it has optimal cleaning efficiency and can really breathe life into old steel products and structures.
Painting of metal structures can be selected in several ways. The two most common methods would be spray painting and sheeting. This is due to the fact that they provide a wide range of metals with long protection and a stunning finish.
Powder coating of metal is used in industries such as
We provide the services of coating specialists who are suitable for some specialized projects. When painting steel structures, various paints can be used. Some examples can be found further on the page. It offers epoxy and polyester types with periodic coating, manual spraying and conveyor system feeding processes. Capable of coating flat materials, pipes, forgings, bars and molds. Specifications include coverage up to 76 inches long and 24 inches in diameter.
Examples of work on the painting of metal products:
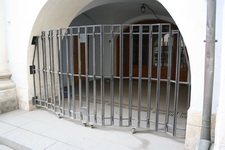

Powder coating in the RAL palette
✔ We paint metal products in any shade of the RAL, RR, NCS palette, the Moscow Color Palette. Decorate with copper, bronze.✔ Paint from and 1 product. We sell powder paint of rare colors from 1 kg.
1 - RAL yellow series | |||||||||||||||||||
2 - RAL Orange Series | |||||||||||||||||||
3 - RAL red series | |||||||||||||||||||
4 - RAL purple series | |||||||||||||||||||
5 - RAL Blue Series | |||||||||||||||||||
6 - RAL green series | |||||||||||||||||||
7 - RAL gray series | |||||||||||||||||||
8 - RAL brown series | |||||||||||||||||||
9 - RAL white, black, metallic | |||||||||||||||||||
The objects
Is paint included in the price? Paint is included. There is no need to pay separately.
What is the maximum product size allowed for powder painting? We carry out powder painting of products up to 12000x1900x1250 mm. Which manufacturers paint do you use?
In the work we use only imported powder paint from leading manufacturers. Do you paint only on the RAL scale or in rare colors too? "PP MetStroy" makes painting in any color RAL (Classic, Effect, Design), RR, NCS, Moscow palette. We sell powder paint from 1 kg (there are many rare shades, others on order).
Detailed Specifications: Powder Coating
A: 2: (s: 4: "TEXT"; s: 14561: "
Powder Coating Price
✔ Prices for painting in Moscow, Moscow region, Lyubertsy district, town of Tomilino, st. Garshina, 26A.. ✔ Cost in St. Petersburg, please check with managers.Powder coating | ||||||||||||
Flat products | ||||||||||||
Characteristics | Quantity, m² | Cost, rub / m² | ||||||||||
Gloss | ANTIK, Matte, Shagreen | |||||||||||
Metal products with dimensions up to (LxWxH) 6000x1700x1300 mm * | from 25 to 100 | 203 | 405 | |||||||||
from 101 to 500 | 192 | upon request | ||||||||||
from 501 to 2000 | 183 | upon request | ||||||||||
Corrugated flat products (Professional sheet) | ||||||||||||
from 25 to 100 | 216 | 405 | ||||||||||
from 101 to 500 | 206 | upon request | ||||||||||
from 501 to 2000 | 196 | upon request | ||||||||||
Profile and long products | ||||||||||||
External perimeter of the product, mm | The cost of painting (Gloss), rub / m. | |||||||||||
Less than 150 | 30 | |||||||||||
151-250 | 54 | |||||||||||
251-350 | 75 | |||||||||||
351-450 | 102 | |||||||||||
451-600 | 129 | |||||||||||
Maximum length of profile products - 6100 mm | ||||||||||||
The cost of painting 1 pog. m of a long product with a perimeter of more than 600 mm \u003d External perimeter x painting cost 1 m² Additional elements | ||||||||||||
Additional elements | ||||||||||||
The cost of painting additional elements - 203 rubles / m² | ||||||||||||
Piece and small items | ||||||||||||
Size, type mm | Cost, rub./ pcs. | |||||||||||
Self-tapping screws | 1.62 | |||||||||||
Small items (fasteners, accessories, souvenirs, other details with dimensions less than 50 mm) depending on the configuration | From 14 to 61 rubles. | |||||||||||
Additional services | ||||||||||||
Name | Units measuring | Cost | ||||||||||
Surface cleaning complete | % of the cost of painting | 50 | ||||||||||
Partial surface cleaning | % of the cost of painting | 15 | ||||||||||
Drilling holes | rub / pcs | 21 | ||||||||||
Heat treatment of oiled metal before painting | % of the cost of painting | 20 | ||||||||||
Primer surface with anticorrosive primer | % of the cost of painting | 80 | ||||||||||
Painting one product in 2 colors | % of the cost of painting | 110 | ||||||||||
Painting in several layers (varnish, primer, two layers of paint) for each layer |
% of the cost of painting | 100 | ||||||||||
Repainting (paint on paint) | % of the cost of painting | 30 | ||||||||||
Volumetric products - (boxes, containers, frames, safes, instrument housings, ducts, coasters, stands, etc.). | rub / m² | 216-297 | ||||||||||
Pasting by a self-adhesive film | % of the cost of painting | 20 | ||||||||||
Luminescent paint RAL 1026/2005/2007/3024/3026/6038 |
% of the cost of painting | 50 | ||||||||||
Cutting to size | rub / rez | from 67 | ||||||||||
Product weight from 50 to 100 kg (Not more than 100 kg) | % of the cost of painting | 50 | ||||||||||
Production of coating samples 200x200 mm | rub / pcs | 1080 | ||||||||||
Terms of execution of orders for painting | ||||||||||||
Order status | Painting time | % Markup | ||||||||||
Planned (not counting the day of receipt) | 3-5 business days | no | ||||||||||
Urgent | 1 day | 50 | ||||||||||
Issue of orders | ||||||||||||
Day of the week | Time hours | Note | ||||||||||
Weekdays | 9.00 - 18.00 | Mandatory availability of the original power of attorney or seal | ||||||||||
Minimum order amount for painting in one color | ||||||||||||
With an order volume of less than 25 m² or 100 linear meters m the cost of painting is equal to the minimum cost of 1 production cycle and is 6700 rubles. | ||||||||||||
Custom products painting | ||||||||||||
When painting non-standard products, the cost of painting is calculated individually | ||||||||||||
"PP MetStroy" produces painting according to modern technologies in compliance with all technological standards for painting metal products. The stages of painting finished products include all the necessary operations and surface preparation for the highest quality result. We work with paints of the world's leading manufacturers on the RAL scale and guarantee that the finished elements will be painted on time. | ||||||||||||
* Prices include VAT |
- The price includes the cost of paint of any color according to the RAL catalog in one layer, work on the preparation of products, application of powder paint.
- You can calculate the cost of manufacturing metal products and structures, additional processing of metal, drilling holes, cutting, packaging, delivery from our specialists by phone or by sending an application.